- By Fawaz AlSahan, CAP
- Special Section
Summary
Fast Forward
- There are different level measurement options for inventory tank gauging. Cost, schedule, and other challenges affect the final technology selection.
- GWR technology was tested in Saudi Aramco for inventory tank gauging with successful results.
- The Saudi Aramco Riyadh Refinery revised the project scope for implementing inventory tank gauging on 42 tanks, and ended up with a simple, cost-effective, and fast project implementation.

Cut the cost, simplify the project, and expedite implementation
There are two internationally recognized standards covering tank gauging in atmospheric tanks. From the American Petroleum Institute, there is API MPMS chapter 3.1B and API MPMS chapter 7, and from the International Organization for Standardization, ISO 4266-1, ISO 4266-4, and ISO 11223. This article is based on API MPMS chapter 3.1B and API MPMS chapter 7, because these two documents provide detailed requirements for inventory applications. API MPMS chapter 3.1B mandates the following requirement for automatic tank gauges (ATGs):
The reading of an ATG to be used for an inventory application should agree with a certified measurement instrument within ±3 mm over the entire range of the ATG.
- The certified measurement instrument should be traceable to the national or international standards and should be provided with a calibration correction table.
- The overall accuracy of an ATG in inventory control service should be within ±25 mm.
- ATGs should provide security to prevent unauthorized adjustment or tampering.
- The level resolution of the transmitted signal is typically 1 mm.
Conventional tank gauging solutions
There are five common automatic tank gauging solutions widely used for both inventory and custody applications.
Manual gauging
This solution is the reference for all other solutions, and it utilizes a dip tape. Manual gauging uses either the innage (from the top flange to the bottom of the tank) or ullage (from the top flange to the top liquid layer) method to measure the total liquid level inside the tank. API MPMS chapter 3.1A covers the procedure and requirement for manual gauging, which is normally three consecutive readings with a difference not exceeding ±3 mm.
Float and tape gauge
This solution uses a float attached to a spring via a perforated tape. The spring provides constant tension, which balances the float on the liquid level. The perforated tape is connected to a mechanical counter assembly.
Servo gauge
The servo gauge uses the displacement measurement principle. A small displacer (weight) on a measuring wire from a drum is accurately positioned and balanced in the liquid medium using a servomotor. These devices can meet the inventory and custody accuracy requirements.
Radar tank gauging
Radar tank gauging (RTG) is the most common solution for tank gauging. It used to be the Saudi Aramco standard tank gauging solution for inventory tanks. This technology is microwave-based, which measures the distance from the top connection to the liquid surface. The two available techniques are frequency modulated continuous wave (FMCW) and time-of-flight time domain reflectometry (TDR). These devices can meet the inventory and custody accuracy requirements.
Hydrostatic tank gauges
A hydrostatic tank gauge (HTG) system has up to three pressure transmitters and one temperature transmitter. Two pressure transmitters are installed close to the bottom of the tank and are used to calculate the density. A third transmitter measures the vapor pressure at the top of the tank to increase the accuracy.
Project initial scope and challenges
One recent tank gauging project at Saudi Aramco Company was scoped to install radar tank gauging with multiple points of temperature measurement on 42 tanks for crude and refined products. Three types of tanks are available: external float, internal float, and fixed-roof tanks. The main challenges addressed during the design stage were:
- Each RTG required excavation for running new and long cables for the signals and for the external power supply, in the large tank farm area.
- A nozzle size of 6 to 8 inches was required for every tank.
- A nozzle was required for the multiple spot temperature transmitter.
- Tanks with internal roofs had to be empty, cleaned, and ventilated to install the new stilling pipes. This meant at least three-to-five years to execute the project.
- New cabinets, hardware, and software installations in the process interface buildings were required, which could mean expansion of existing buildings or construction of new ones.
- RTG required factory acceptance testing (FAT), which adds to the project schedule and cost.
- The project execution would take years, including its high cost.
GWR technology for inventory tank gauging
Principle of operation
Guided wave radar (GWR) or time domain reflectometry is a two-wire microwave level instrument that transmits a radar signal down a metallic wave guide (single-rod/cable, twin rod, cable, or coaxial rod). The instrument principle of operation is time of flight.
V = C / √K
Where
V = pulse velocity in service
C = pulse velocity in air = 300,000 km/sec
K = dielectric constant
The signal transient time to and from the liquid surface will determine the level measurement.
GWR advantages
GWR technology has many advantages, which make it an attractive option for inventory tank gauging:
- The GWR level instrument is a two-wire transmitter and does not require an external power supply.
- GWR is a very economical choice in terms of capital and operating expenditures.
- GWR can be installed while the atmospheric storage tank is in service.
- GWR is "plug and play" and a maintenance-friendly technology.
- The GWR cable version can be extended up to 75 meters high.
- GWR is insensitive to dielectric changes and works for fluid with a low dielectric constant.
- GWR is available with different process connection types and sizes.
- A GWR rod/cable can be cut to fit the length (or height) required.
- A GWR instrument can provide both total hydrocarbon level and water interface level.
- GWR has different and open communication protocols\, such as analog 4-20 mA, Foundation fieldbus, and wireless.
- GWR can have an intrinsic lab accuracy between 2 mm and 3 mm, and a 25 mm installed accuracy depending on the vendor and measuring distance.
- GWR vendors can provide five-point calibration for each GWR.
- The technology is in compliance with all API MPMS chapter 3.1B requirements highlighted above.
- GWR will eliminate the conventional RTG proprietary hardware and system component.
- Due to its simplicity, a FAT is not necessary.
- GWR can be installed with or without stilling piping.
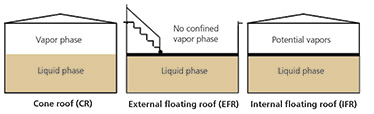
GWR piloting and test results
A plan was set to pilot four GWR level instruments from two different manufacturers on different types of tanks with different refinery products, and to monitor the performance over one year. Over this period, the operation team conducted frequent manual gauging (three times per test) to check the installed accuracy of the GWR.
Before proceeding with the field test, the selected vendors were asked:
- to confirm that the intrinsic accuracy of their GWR is within ±3 mm (±1/8 inch). Also, every vendor had to provide five-point calibration of each GWR to confirm the said accuracy. Both vendors provided the confirmation and data required.
- to provide a certificate of the reference-certified instrument, illustrating traceability to national or international standards. The vendors provided certificates for traceability to German accreditation body
DAkkS. - to confirm that the GWR transmitters have write protection. Both vendors confirmed and illustrated this feature for their GWR instruments.
It was also mutually agreed with the two GWR vendors to check and confirm the following after the installation and commissioning:
- the overall accuracy of the GWR, which should be within ±25 mm (±1 inch)
- the reading difference between the local transmitter display and remote DCS reading, which should be within 1 mm
Accordingly, four tanks were selected to proceed with the field trial. The figure 7 table highlights the data.
The sketches in figure 8 represent the installation setup for the GWR instruments on the three types of tanks (from the left: external roof, internal roof, and cone roof).
After commissioning, the echo curve was collected for each transmitter to confirm a strong echo for each GWR, with no loss of signal and no interference (figures 10 and 11).
Over one year, the refinery operation team conducted manual dipping to check the reading accuracy of the installed GWR instruments. The data over the year has clearly demonstrated that the accuracy is within the required ±25 mm for inventory tank gauging applications. A sample of the data collected is in figure 12.
Project scope revision
The successful results of piloting GWR for the inventory tank gauging application revealed a new and suitable solution for Saudi Aramco's Riyadh Refinery project. The project scope was revised to mandate GWR for the project and eliminate all the complexity and constructability challenges. The vendor selection was biding based, since the GWR instruments from both vendors demonstrated a superior and equal performance. The project's final scope of work was revised as follows:
Measurement technology and setup:
- GWR shall be used for inventory tank gauging for the Riyadh Refinery project.
- For tanks with no stilling piping (e.g., tanks with a cone or internal floating roof), there is no need to install stilling pipes.
- For temperature measurement and since this application is inventory, a spot temperature sensor shall be used as it is allowed by API MPMS chapter 7.
- A pressure transmitter shall be installed at the bottom of each tank to assist in mass calculations.
Communication protocol: Foundation Fieldbus (FF):
- The existing FF segments in the refinery tank farm have been verified and found feasible to accommodate the new GWR instruments in this project.
- The existing asset management platform in the RR tank farm (i.e., PRM from Yokogawa) will be used for maintenance.
Tank inventory calculations: DCS shall be used, as it has the capability to perform the inventory calculations addressed in API MPMS chapter 12.1.1.
The Yokogawa Tank Inventory Management Module was configured as the existing DCS at the refinery. This step has eliminated proprietary hardware and software for the tank inventory calculations.
Economical solution
The journey of the Saudi Aramco tank gauging project has resulted in a simple, reliable, and highly economical system for inventory tank gauging. This solution demonstrated full compliance with API MPMS chapter 3.1B in terms of accuracy and performance. Moreover, it provides a versatile solution, which allows different hardware and communication protocols to be used and allows DCS as a platform for software inventory calculations.
It is important to highlight that GWR has fundamental rules set by the manufacturers for selection, installation, and commissioning. Following these rules will guarantee successful performance. Deviating from these requirements can generate unpleasant challenges and errors in measurement.
The GWR success story has also opened another opportunity for using two-wire noncontact radar for inventory tank gauging, as these noncontact radar instruments have the capability to meet the requirements of API MPMS chapter 3.1B. They can be very useful in applications like molten sulfur and asphalt.
This success story had an impact not only on the Riyadh Refinery project, but also on Saudi Aramco standards, which have been revised to specify two-wire GWR for inventory tank gauging, as long as the vendors demonstrate a full compliance to API MPMS chapter 3.1B requirements.
ACKNOWLEDGMENT
The author would like to acknowledge the support of the Saudi Aramco Riyadh Refinery management, and to acknowledge Riyadh Refinery automation engineers Fawaz AlHadlaq and Khalid Batoq for their assistance in preparing this article and their commitment to conducting the pilot testing and building a new milestone.
Reader Feedback
We want to hear from you! Please send us your comments and questions about this topic to InTechmagazine@isa.org.