- By Stefan Zippel
- Process Automation
Summary
Fast Forward
- The Industry 4.0 transformation of the process industry is a journey to become innovative, flexible, data-driven, and agile organizations.
- The right combination of legacy process industry systems and new Industry 4.0 technology is the foundation to enhance the availability of information and improve decision making.
- Industry 4.0 frees employees to use their creativity, innovation, imagination, and intuition to optimize processes, increase profits, lower costs, and minimize risks in the process industry.
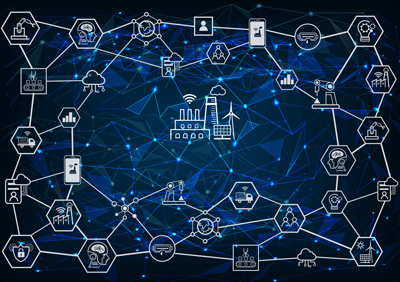
Transforming the process industry with Industry 4.0
When the Industry 4.0 working group presented its results at the Hannover Fair in 2013, it hardly made any impression within the process industry. Following my webinar, "Industry 4.0: A Blueprint for Achieving a Dynamic Smart Factory" (produced by Marcus Evans in partnership with Advantech in June 2017), two questions remained unanswered:
- What is the strategy and road map of initiatives in 4.0 for chemical or seeds facilities?
- Is there an Industry 4.0 standard for process industries like the chemical industry?
In my role as an Industry 4.0 architect, I still hear questions regularly. This shows that confusion still abounds.
Industry 4.0 and the process industry has a difficult past
The use of heavily automated production as well as centralized control and data collection dates back to the 1960s. The first such industrial control computer system was at the Texaco Port Arthur refinery in Texas in 1959. At that time, it was clear that industry standards were needed to ensure consistent terminology and operation models. Subsequently, the ISA-95 standard was established, from which IEC 62264 (DIN EN 62264) was formulated. The process industry was not the only one to follow the ISA-95 standard.
ISA-95 already widely used
With ISA-95, most process industry facilities achieve a nearly fully automated production process, where assets are connected to a central control system (e.g., distributed control systems [DCSs] and supervisory control and data acquisition [SCADA]) and historians/manufacturing execution systems (MESs) are often deployed. Although other industries also deploy automated assets, often with programmable logic controller (PLC) or computer numeric control, they lack the interconnected environment we know from the process industry. There is a gap between the individual assets and higher-level functionality. As a discrete manufacturer, the Volkswagen Group demonstrates in the YouTube video, "Industry 4.0 in the Volkswagen Group," the long-established concept of the central control room as part of its Industry 4.0 strategy.
Looking at Industry 4.0 as a journey, the process industry is already flying, while other industries are only now checking in.
Industry 4.0 and existing standards
Conforming to ISA-95 is certainly an advantage for the process industry, but it has also been an obstacle when evaluating Industry 4.0. Strong biases toward existing standards warp the understanding of the value of Industry 4.0 to the process industry. It was unfortunate that most of the initial use cases for Industry 4.0 were in the automotive industry and did not represent the reality in the process industry.
Additionally, the hype around the Internet of Things (IoT) failed to look at the high connectivity already present in the process industry. Even the early data analytics models failed to highlight their advantages over principles like real-time optimization. In short, Industry 4.0 failed to show how it would raise profit margins, lower operating costs, and manage risks better than the existing standards used in the process industry.
It was not until 2015 that organizations like NAMUR (User Association of Automation Technology in Process Industries, www.namur.net/en) started exploring the first applications of Industry 4.0 in the process industry.
Not enough focus on people and processes
The focus of Industry 4.0 has been on the technology, connecting assets and collecting data. But similar technology has been used in the process industry for decades. Instead of trying to capture the attention of the process industry with tools, the focus should have been on using Industry 4.0 to make the right decisions, at the right times-optimizing processes, maximizing profits, and minimizing risks.
Technology is only an enabler. Industry 4.0 is about the processes and structure within an organization and across its value chains. It is about the human element and how our workers can truly add value with their creativity and innovation. This understanding of Industry 4.0 has gained significant traction since I first became involved in 2014.
New process industry use cases
Example use cases from the process industry (Covestry, Lonza, HPE and Texmark) were highlighted in several keynotes in the recent Industry of Things World conference in Berlin, illustrating how conforming to ISA-95 can quickly bring benefits from enhanced data collection. A few use cases showed how mobile devices brought real-time data into the field when checking critical assets, instead of keeping that information locked away in a control room. Others showcased how digitized dashboards improved on paper-based communication channels. All of these improvements were to processes. The benefits were realized by following the Industry 4.0 principles of improved communication and open information sharing.
Industry 4.0 has a future in the process industry
Until now, Industry 4.0 did not clearly show how it could benefit the process industry, because the focus appeared to be on the technology and the hype around how many jobs would be lost. However, Industry 4.0 is about establishing an active collaborative network, both within organizations and throughout their value chains: people and technology connected by digital threads and limitless information exchange.
The process industry is full of hierarchical organizations with isolated operational silos and information stored behind "locked doors." The way forward is clearly a solution-oriented network of people, tools, and shared information across boundaries, supported by the process industry's existing standards and technologies.
Implementing Industry 4.0
Why so many projects fail
In my experience, organizations do not start at the beginning, by understanding their processes. Instead, they start with reports or dashboards already in mind. But the solutions selected to deliver those outcomes rarely survive the first contact with reality. These projects fail, because they fall into a constant cycle of modifications and rebuilds, as each step in the processes throws up unforeseen issues, causing delays and increased costs.
Instead of a custom Industry 4.0 strategy based on the existing processes and system landscape within a company, many have a checklist of technologies they want to use, whether their processes require them or not: IoT/IIoT, AI/ML, mobile devices, augmented reality (AR)/virtual reality (VR), cloud, etc.
First steps for a successful implementation
Your experienced workforce is critical to identifying both low-hanging fruit and your biggest pain points.
- Map every step in every process and every system that is used. You need to understand what each step or system is used for, what is done, why it is done, and how it is done.
- See what works well and which standards are used. But more importantly, see what is not working and which standards are not used.
Common low-hanging fruit
Plant communication: Digitize paper-based plant data into dashboards to transform existing analog data into real-time information, so you can use this knowledge. This becomes a powerful asset for artificial intelligence (AI) and machine learning (ML) implementations. Dashboards on screens, laptops, and mobile devices not only let you make data-driven decisions in the moment, but also enable you to see what works and what does not.
Constant process optimization: Using collected data to drive plant optimization is not new. Data-driven methods like Six Sigma or Lean in combination with a data historian are a match made in heaven. A historian can provide ample data for your measurement and analysis phase, allowing you to quickly perform a comprehensive root-cause analysis and review sustainability. Real-time optimization applications are available, but the complexity, skills required, and cost involved mean they are not suitable for all situations.
Interfaces between systems: Many companies have a variety of systems in use, such as ERP, SCM, CRM, QMS, LIMS, WMS, MES, DCS/SCADA, and HRM systems. But most are isolated where data and information exchange is rudimentary-paper-based or via text email at best. Start creating your company's digital thread by setting up interfaces based on standards like OPC-UA, Message Queuing Telemetry Transport (MQTT), Rest, or Open Database Connectivity (ODBC) in combination with ETL (extract, transform, load) or ELT (extract, load, transform).
Predictive maintenance, or using machine learning to produce a maintenance model, is not a short-term project. In fact, one company admitted in its 2018 keynote that its machine learning project was yet to produce a working model, even after three years. Its machines are scheduled for replacement in two years.
Do not jump into a machine learning solution if you cannot solve the problem without it. Leverage your employee's experience first-mechanics often "know" whether their machines are running well, because they have a model in their head of what they need to keep an eye on. Tap into their experience and monitor what they suggest.
For example, a pump will break at some stage. We know how much pressure the pump generates at a given power consumption. An experienced employee keeps an eye on these values and knows that when power consumption rises, the pump will break in the near future. It is easy to monitor these two values (power and pressure) and trigger an alarm in your central control system to signal that maintenance is needed.
Looking forward: Will the process industry fully embrace Industry 4.0?
Industry 4.0 will free humans from having to compete with machines, especially on speed and quality in repetitive tasks. Instead, we can take advantage of human strengths like creativity, innovation, imagination, intuition, and ethics to full effect. But there are many small steps along this Industry 4.0 journey.
Work with existing systems and architecture
A form of IoT already exists in process industry plants, and even in discrete manufacturing assets like molding lines or die casting cells. "The Internet of Things (IoT) is the network of physical devices and other items embedded with electronics, software, sensors, actuators, and connectivity which enables these things to connect, collect, and exchange data." (Wikipedia)
In the past, to record a new measurement, you had to purchase expensive hardware, wait for a shutdown, wire it in, rewrite the control program, test the code in simulation, load the new program, and hope that the change did not reduce productivity. Because of the costs and risks involved, updates like these were rarely done, resulting in many missed opportunities to optimize processes to decrease costs and increase profit margins.
Integrate IoT devices
IoT devices are comparably cheaper and easy to install, customize, and update. They can communicate with data collection systems without the need to run cables and rework production lines. The true power of IoT devices is to enhance data collection capabilities without disrupting production.
Enhance existing data collection
In edge computing, computation is done by the device (the sensor or actuator) itself or by a nearby computer system and not in a remote data center or the cloud. You can use edge computing with existing technology like DCS/SCADA and historian/MES systems. Existing infrastructure like DCS/SCADA and historians is valuable, well designed, and reliable. They belong in any Industry 4.0 architecture, but they are not designed for real-time analysis of data to identify patterns. Edge computing working with these existing systems can analyze patterns and trigger actionable states, such as alarms.
Implement data analytics, AI, ML, and digital twins
As Greg Hanson, CTO and vice president at Informatica, put it, "If you put garbage [data] in, you'll get garbage [data] out." Too many companies fail to use data analytics effectively in their quest to add value, minimize risk, increase profits, and lower costs. The TV series Star Trek: The Next Generation shows how employees can use data analytics to add value. When crew members need to make a decision, they ask their computer (AI) questions to leverage the vast amount of stored information and determine the best course of action or to phrase further questions. This open information exchange helps the crew make the right decisions at the right times, and the AI learns more about those situations.
Value of data analytics
There are many applications of data analytics in chemical plant engineering, product development, customer service, and service or product development. One concrete example is using AR/VR or mobile devices to guide and assist technicians. Here are some ways that data analytics can add value:
Predictive maintenance: Similar to predictive plant control, real-time data is used to predict when equipment will fail. Instead of performing maintenance on an arbitrary schedule, you do it only when it is necessary, guided by past experience. You are more likely to identify equipment failure before it happens and better manage the risks involved. The key to success here is the experience of your maintenance staff.
Real-time process optimization and predictive control: Deploying AI/ML can deepen the understanding of how a plant operates. Building upon your employees' past experience, predictive operational control and real-time process optimization enhanced by AI/ML will further improve quality, reduce safety issues, and optimize energy and raw material consumption.
Energy management: The process industry relies on utilities (e.g., electricity, steam, gas, and water), and energy management is necessary to limit costs. Today, energy management focuses on the collection of energy data to achieve certifications like ISO-50001, which are typically used for tax benefits.
If you combine this information with systems like MES, enterprise resource planning (ERP), and supply chain management, it becomes easy to predict the energy consumption based on the scheduled activities. You can use these predictions to negotiate shorter-term energy contracts-freedom to choose the best offers can bring significant savings. Plus, you can analyze process data together with energy data to optimize your production process to reduce your energy consumption.
Support at all levels
Developing your own custom Industry 4.0 architecture is one part of the picture. Industry 4.0 needs your support as it evolves to adapt to new challenges and use cases. Chief officers, such as CIOs, CTOs or CDOs, play critical roles in the transformation to Industry 4.0.
I agree with Nick Ismail in his recent article, "Artificial intelligence: Data will be the differentiator in the marketplace," where he said that the CIO is essentially responsible for the "support and sustain" side of things, while the CTO is responsible for translating the new business requirements to technical requirements. All parties involved should learn about existing standards and participate in the development of new or updated standards.
Support from evolving standards
ISA-95 is a cornerstone in an Industry 4.0 architecture, as underlined by Charlie Gifford and David Daff in "ISA-95 evolves to support smart manufacturing and IIoT." I am personally developing an ISA-95-based architecture as illustrated in the figure. This lets my organization reap the rewards of using an established standard, helps with the IT-OT convergence, and manages the flow of the data and information between the operational functions.
Quick wins give your Industry 4.0 project momentum:
- Analyze and document processes and infrastructure. Complete understanding is required before new technology or processes are introduced. Bringing employees onboard will be easier, and you may discover many easy optimizations.
- Build inexpensive interfaces between your existing infrastructure and processes to collect and share data.
- Create digital dashboards to streamline communication using the cost-effective edge computing and IoT technologies. Make this information available in real time everywhere to make better decisions.
- Monitor and optimize your energy use to achieve certifications and negotiate more appropriate energy contracts.
- Leverage your experienced employees' knowledge to improve upon or prevent expensive maintenance on equipment.
Gradual transformation
Advanced applications in data science will slowly become more common, working alongside existing systems, such as DCS/SCADA, manufacturing operations management, and enterprise resource planning, and Internet of Things devices will be used increasingly often to enhance existing data collection systems. If correctly deployed, they will fundamentally transform how the process industry operates in the long term.
Data models need to be trained over time before they can actually contribute positively. They also have to be validated and constantly improved and adjusted to stay relevant. So, they are not a quick fix to lower costs. Both the new technology and analytics require highly trained new workers, as well as your experienced staff who understand the "old world," the processes and technology that you use now.
Siloed responsibilities and old barriers must be destroyed and replaced with open collaboration for Industry 4.0 to succeed. Industry 4.0 is absolutely not going to reduce your workforce. To be effective, you will need to hire skilled personnel to keep your Industry 4.0 initiative alive and well and retrain your existing workforce, so they become an enthusiastic part of your Industry 4.0 strategy. This massive transformation will not happen overnight, but it is happening gradually in the process industry, right now.
Reader Feedback
We want to hear from you! Please send us your comments and questions about this topic to InTechmagazine@isa.org.