- By Megan Buntain
- Connectivity & Cybersecurity
Summary
- Cloud computing is being rapidly adopted to support improved production agility and more distributed work teams.
- Previous barriers to cloud computing are being overcome with hybrid and pure cloud approaches.
- Microsoft and AWS are increasing the breadth of industry-specific services and learning quickly which are viable.
COVID-19 is accelerating IT cloud investments to deliver the innovations required to cope with the pandemic and other market disruptions.
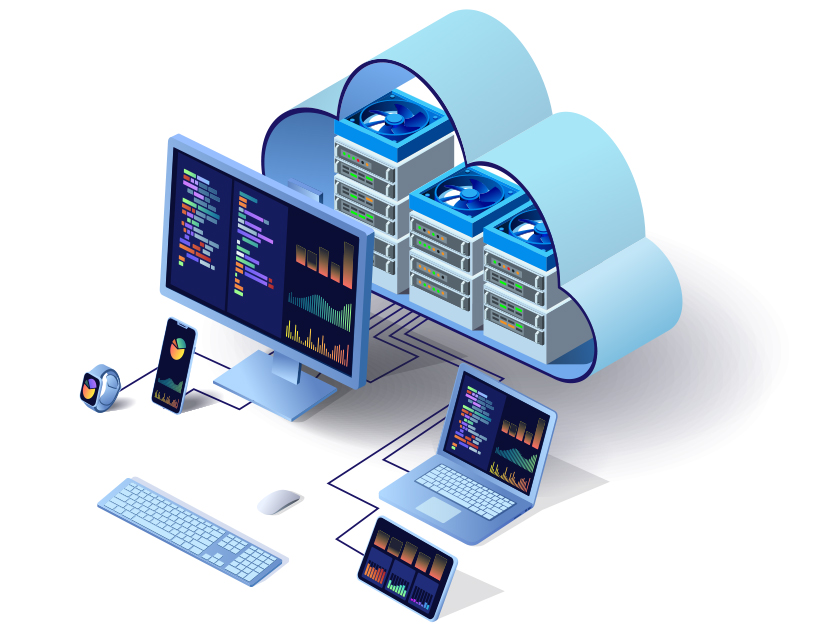
Process manufacturing encompasses critical industries supplying the world’s consumers and businesses with energy, food, water, and other crucial and life-supporting goods. With the spread of COVID-19, industry faced a tidal wave of challenges to manage production in this volatile environment.
New levels of agility were needed to meet extreme fluctuations in global demand for products and services, and the pandemic also exposed risks in vulnerable supply chains. As a result, many manufacturers accelerated investments in information technology (IT), specifically in cloud computing, advanced analytics, and digital factory initiatives. The theory was that without access to real-time insights for improved decision making, manufacturers would be left flat footed when trying to respond to rapidly changing market conditions.
Some of these investments in agile models and digital factories were already starting to take shape before the pandemic. In May 2019, McKinsey reported that “many leaders in asset-heavy companies hear about agility through their internal digital teams . . . Companies often establish special units—digital factories, garages, accelerators, incubators, studios, labs—to execute at speed . . . then scale up.”
Later in 2019, IDC forecast that half of manufacturing companies worldwide would invest in supply chain resiliency and artificial intelligence (AI) before the end of 2021 to achieve productivity improvements of up to 15 percent. To cope with the COVID-19 pandemic, factories began accelerating the pace of these investments to:
- achieve improved production scheduling.
- empower employees to collaborate productively while working from home.
- gain predictive insights from advanced analytics to ensure process improvements could be implemented proactively.
The results of a February 2021 survey titled “Fast Forward to Future Factories” by the U.S.-based Manufacturing Leadership Council (MLC) backs this up. “When the MLC first surveyed its membership to understand more about the pandemic’s potential impact on [Manufacturing 4.0] adoption during the height of the first COVID wave in April and May of last year, just over 50 percent of respondents indicated that it had prompted them to accelerate their adoption of M4.0 technologies across their organizations and factory floors . . . The MLC’s latest research, however, clearly indicates that this acceleration surge was far from a temporary fix. Over 40 percent of respondents in our latest survey now confirm that they will continue to accelerate their rate of M4.0 adoption for the foreseeable future. For two in five manufacturers, this marks an inflection point in M4.0 adoption that is set to drive digital transformation faster than ever before.” These predictions and surveys illuminate a problem faced by many manufacturers: getting more value from existing data.
Cloud computing drives insights from data
Access to operational data and the analytics tools needed to find the proverbial needle in the haystack, or more accurately the thousands of needles in the millions on haystacks, are imperative to achieve agile and efficient operations. More data from automation, human-machine interfaces, and supervisory control and data acquisition (SCADA) systems is coming online daily. To cope with this deluge of data, industrial companies are turning to cloud computing for its near-limitless storage capacity and computing capability, along with ease of access for remote users worldwide.
For example, in many operational analytics programs, teams begin with a goal of achieving widespread access to plant-level data, and eventually to enterprise-wide reporting on key performance indicators. With global reporting in place, the next wave of innovation in the program typically aims to harness the transformational potential of machine learning–driven analyses, which can be provided by cloud-based deployment (figure 1).
For example, consider the potential of a standardized method of predicting downtime events for hundreds to thousands of assets—such as pumps, compressors, or heat exchangers. What is the prospective return for productivity improvement in your plants that can be achieved through downtime avoidance, or by extending the life cycle of expensive-to-replace assets by months or years? Next, consider the impact on agile manufacturing initiatives when those analyses are retrained and redeployed on the fly and at scale as production needs or operating conditions change. These and other improvements are possible, and cloud computing often provides a quicker path to implementation.
Hurdling cloud barriers
To achieve the goal of optimized operations, the barriers to adopting cloud technologies must be carefully evaluated and overcome. The common challenges cited by operational leaders involve three areas of concern: cybersecurity and data protection, network connectivity and latency, and the change management required to foster more IT and operational technology (OT) collaboration. There are numerous resources available from industry, analyst, and vendor publications outlining the best practices for addressing each of these issues.
What is common across most approaches is a hybrid world for many years to come, where some operational data remains stored within the corporate network, while other data migrates to the cloud.
Data on the corporate network can still be securely accessed from analytics applications running in the cloud, with other data sets loaded or streamed directly to the cloud, while using the best models for cybersecurity threat prevention. For network connectivity, capabilities such as edge computing and smart caching of data in the cloud bring high-speed analytic results for many use cases.
Finally, the cloud is the place where OT and IT teams will inevitably come together. When a manufacturer decides to transform its end-to-end operations, both OT and IT will need access to data and the ability to create automated business processes and workflows across supply chain, operations, financial, and customer management systems.
This end-to-end view is best achieved by intelligent use of the cloud. This requires a partnership with IT supporting the underlying technology infrastructure, while OT ensures the most critical data and applications—those driving production—are not left out of the digital transformation effort (figure 2).
The following examples show how three different process manufacturers are dealing with this issue by implementing cloud-based solutions for advanced analytics.
Driving agility with the cloud
A global consumer packaged goods manufacturer is halfway through a three-year program to implement digital factories and a program called “futures engineering.” Engineers and subject-matter experts in over 300 factories are empowered with self-service industrial analytics applications for improved decision making. The first phase of the initiative involves replicating critical OT data to the cloud data platform. From there, engineers will be empowered with near-real time analytics tools to find time periods of interest; cleanse, contextualize, and trend the data; and operationalize prediction models. These actions will continuously improve quality and yield outcomes, each of which can be easily shared with and rolled out globally to peers. This manufacturer chose to drive its agile and digital programs from its employees’ needs, and then work backward to design the underlying cloud computing infrastructure.
Another example is OT and IT leaders at a multinational chemical manufacturer coming together to launch a common vision for OT and IT convergence, designed to improve agility in production scheduling. This manufacturer deployed a hybrid approach building on its global on-premises OT data infrastructure by adding cloud-based analytics tools. This enabled its engineers to easily connect to the data and find insights to achieve plant and companywide reliability, productivity, and sustainability goals with maximum flexibility. This manufacturer also put its people at the center of its strategy, and then rallied the team to align OT and IT goals, with joint execution plans in support of employees.
A final example is an energy company that took the leap over the past two years to implement a pure cloud model. The company transformed operations by moving from multiple SCADA systems, including over 25 historian servers managed by business operations and IT teams at a local level, to an enterprise-wide SCADA system in the cloud. The goal was to simplify the data strategy and access by standardizing SCADA and historian data systems in a single cloud platform, enabling Industrial Internet of Things (IIoT) and machine-learning initiatives.
As these examples show, process manufacturers are rapidly transitioning at least some of their data storage to the cloud. AWS, Microsoft, and other software giants are joining the party by offering complementary offerings (see sidebar: Cloud Providers Launch Data Services for Industrial Analytics).
Gaining insights
Whether an organization’s approach to cloud computing is all in or the more common hybrid approach, the cloud is quickly becoming a foundational part of agile manufacturing and a critical enabler for quickly achieving returns. My company works with hundreds of process manufacturers to accelerate the impact they are having with advanced analytics, giving us a front row seat to best practices. The most important thing we have learned is that manufacturers can achieve gains from analytics as they move to the cloud.
The good news is that it is not necessary to move or aggregate all operational data in the cloud or a data lake to get started. Instead, analytics tools can be deployed in minutes or hours using a software-as-a-service model, with secure connections made to on-premises process data (figure 3).
From that quick starting place, engineers and subject-matter experts can create high-value insights on the existing data, wherever it resides. As requirements evolve and the need to leverage more cloud capabilities emerges, process and contextual data can be stored in the cloud, with analyses continuing at greater scale and with increased impact.
All figures courtesy of Seeq.
Resources
“The quest for the most magical algorithm”
“Analytics for predictive, preventative maintenance”
“Analytics next: Beyond spreadsheets”
Cloud Providers Launch Data Services for Industrial Analytics
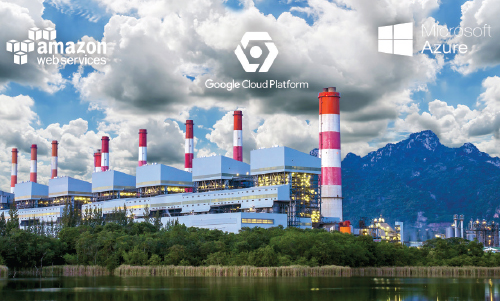
To meet the urgent demands from the process industry, cloud providers—specifically Microsoft and Amazon—are investing in manufacturing as a priority market. Both companies are launching new cloud services in the industrial platforms and analytics category.
Kevin Prouty, group VP of energy and manufacturing insights at IDC, describes the evolution of both companies’ approaches in a December 2020 report, “The Battle of the Operations Hyper-Platforms.” “Since the mid-eighties, Microsoft has been the dominant player in the operational software space. Microsoft has been the foundation for OPC and the majority of operational software used to run industrial operations. But after AWS’s re:Invent 2020, plus the in-the-trenches ecosystem building that AWS has been doing over the last few years, Microsoft now has a real rival in the operations platform space. AWS has always had an innovation bent to its approach to OT. AWS has taken all of the individual products like AWS gateway appliances, IoT products, vision systems, and AWS AI/ML products into a single industrial framework.”
Cloud providers have heavily leveraged their expertise in IoT to develop services for process manufacturers. This IoT-centric approach, very much tuned to greenfield IoT scenarios, includes services for IoT data ingestion, edge computing and applications, optimized data queries for business intelligence applications for enterprise reporting, ML services for anomaly detection, computer vision, and others.
Microsoft Azure Time Series Insights Gen2 and Amazon Timestream are optimized for IoT data, which must be aggregated or preprocessed for optimal query performance. This is not yet an optimal approach for industrial analytics, because important context and meaning can be lost unless one builds analyses using raw, high-fidelity data. These services are rapidly evolving as both Microsoft and Amazon get direct customer feedback; the investment in these purpose-built services will continue to grow.
As an advanced analytics software provider, our company sees a significant near-term opportunity for gaining immediate value from industrial data in brownfield deployments, specifically by adding analytics-driven value to the existing OT data infrastructure.IDC forecasts that factories with more than 500 employees are generating 1 TB/day of data on average. Most manufacturers are already creating, storing, historizing, and processing large volumes of data, yet these companies are challenged to achieve insights at enterprise scale, the classic data rich and information poor conundrum.
Reader Feedback
We want to hear from you! Please send us your comments and questions about this topic to InTechmagazine@isa.org.