- By Bill Lydon
- Features
Summary
From transistors to the brink of Industry 4.0
By Bill Lydon
Since ISA’s founding in 1945, technology has leapt forward, bounding across the decades to change the world. Industrial automation technology has changed no less than technology for transportation, communication, and commerce, and it has indeed borrowed heavily from innovations in those fields. Now, 75 years later, we are on the brink of the Fourth Industrial Revolution, called Industry 4.0, and a wide range of products, methods, plans, and architectures have allowed automation and controls professionals to step ever onward. Here are the top technology milestones that have marked their path. Below are some of the titans of automation technology—ISA members and others—who furthered the tech, optimized it for industrial operations, and supported others in applying it.
Semiconductors and Moore’s law
The first low-cost junction transistor widely available was the CK722, a PNP germanium small-signal unit from Raytheon, introduced in early 1953 for $7.60 each. Putting cost in perspective, Texas Instruments of Dallas and Texas and Industrial Development Engineering Associates (I.D.E.A.) of Indianapolis, Ind., collaborated on creating the Regency TR-1, the world’s first commercially produced transistor radio. When it was released in 1954, the Regency TR-1 cost $49.95 in U.S. dollars (approximately $476 in 2019 U.S. dollars).
Transistors made possible electronic industrial controllers in the 1950s that over time supplanted the application of many pneumatic or air-based controllers of the 1920s and ‘30s.
The cost of solid-state electronics is a history of delivering more power at lower cost. It was expressed in Moore’s law, which has stood the test of time since it was first defined by Gordon Moore, the cofounder of Fairchild Semiconductor and CEO of Intel. In a 1965 paper, he described a doubling every year in the number of components per integrated circuit, and projected this rate of growth would continue for at least another decade. Moore’s law continues to drive computing technology as evidenced by the sophistication and miniaturization of commercial and industrial devices.
The Internet of Things (IoT) is possible because of continued high-performance electronics and processors that continue to get smaller in size and lower in price.
Programmable logic controller (PLC)
Richard Morley, a Bedford engineer, is credited with the original design. He and his team of engineers created a solid-state, sequential logic solver, designed for factory automation and continuous processing applications: the first practical programmable logic controller. It was called the “Modicon 084,” because it was the 84th project at Bedford Associates. Upon learning of GM’s requirements, the company demonstrated the Modicon 084 to General Motor’s Hydramatic Division in November 1969.
Ladder Logic Programming was a huge advantage for working electricians. Much like spreadsheets that later empowered accountants and others, users could program a computer in an easy-to-understand way. Bedford Associates’ Ladder Logic incorporated symbols from electrical engineering to depict sequences of operations. In his article, “Ladder Logic Languishing?” published in the April l992 issue of Manufacturing Systems, inventor Morley recalled:
“Ladder Logic, as a control language, was first used in conjunction with silicon devices around 1969 at Bedford Associates. To support the control language, a hardware platform was devised that had three constituent elements: a dual-ported memory, a logic solver, and a general-purpose computer. Early at Modicon, we used a degenerate form of ladder representation. The great advantage was that the language could be understood by any working electrician in the world. Later the language was expanded to multi-node, and additional functions were added . . . Ladder Logic functionality and PLC adaptability quickly spawned an entire industry.”
The advantage that the PLC brought to the control industry was the ability to program the system, which could not be accomplished with electromagnetic relay panels. The panels had to be rewired when control schemes changed. In contrast, the new PLC could be changed much more easily and faster, and also had the advantage of a much smaller footprint.
Distributed control system (DCS) architecture
About the same time in the mid-1970s, Yokogawa in Japan introduced a distributed control system called the Centum. The Yokogawa Centum and Honeywell TDC 2000 were based on the concept that several microprocessor-based loop controllers could be controlled by supervisory minicomputers. The operator would have a push-button, cathode ray tube (CRT) based display rather than an annunciator panel. The controllers would be connected together on a data highway that would carry the information from the various nodes or stations. The highway, or bus, would serve as a signal route. The design would move the controllers back to the process, shorten the control loops, and save on wiring costs.
Personal computer (PC)
Human-machine interface (HMI)
The development of human-machine interfaces in process control began with a CRT-based system where an operator could read the relative position of process variables “at a glance,” allowing the operator to develop a pattern recognition method of analyzing the current plant operating situation. Honeywell’s TDC 2000, which arrived in 1975, drastically changed the pace of operator console development.
The availability of PCs running DOS and using third-party graphic image software spawned a new breed of HMI solutions around 1985. New companies included Intellution, Iconics, and USDATA.
The next big step was in 1987 when Wonderware introduced InTouch, the first Microsoft Windows–based HMI that added significant features and open interfaces to information technology (IT) and business systems.
Microsoft Windows
Microsoft introduced Windows on 20 November 1985 as a graphical operating system shell for MS-DOS in response to the growing interest in graphical user interfaces (GUIs). Microsoft Windows was a complete, integrated operating system that dominated the world’s PC market with more than 90 percent of market share, overtaking Mac OS, which was introduced in 1984. On PCs, Windows is still the most popular operating system.
Microsoft Windows’ rich environment spawned a large ecosystem of developers who wrote software for a wide range of applications. These included databases, analysis, advanced control, manufacturing execution systems (MESs), batch management, production tracking, and historians.
Microsoft Windows became the way to bridge real-time plant operations with IT and business systems for more unified and coordinated manufacturing and production. The Microsoft Windows operating system platform allowed users to leverage standard IT tools to analyze manufacturing data and share production and plant information seamlessly with business systems. Windows provided the platform for development of OPC, which significantly simplified software drivers for industrial networks and equipment interfaces.
Data historians
Open industrial networks
Starting in 1979, Modbus enabled communication among many devices from multiple vendors by leveraging the RS-485 standard. The standard defined the electrical characteristics of drivers and receivers to use in multidrop, serial communications systems to connect a wide range of controllers, sensors, instrumentation, PID controllers, motor drives, and other devices. Modbus is still prevalent in products, manufacturing, and process plant applications.
In the late 1980s and into the 1990s, there was a proliferation of fieldbus communication standards. Prominent ones that survived include DeviceNet, Profibus, SERCOS, ASi (Actuator Sensor Interface), Foundation Fieldbus, and HART (Highway Addressable Remote Transducer). The HART Communication Protocol, the only one not purely digital, is a hybrid analog + digital industrial automation open protocol. Its most notable advantage is that it can communicate over legacy 4–20 mA analog instrumentation current loops, sharing the pair of wires used by the analog-only host systems.
ISA-88 batch control standards
ISA-88 provides a consistent set of standards and terminology for batch control and defines the physical model, procedures, and recipes. The standards address a wide range of needs, including creating a universal model for batch control, common means for communicating difficulty in expressing user requirements, integration among batch automation suppliers, and simplification of batch control configuration. ISA-88 has been instrumental in bridging all aspects of batch production from the plant floor to enterprise systems. It is worth noting that the PackML standard uses ISA-88.
ISA-95 enterprise-control system integration standards
ISA-95 (ANSI/ISA-95) provides consistent terminology and object models that are foundational for supplier and manufacturer communications. By helping to define the boundaries between enterprise systems and control systems, ISA-95 models clarify application functionality and how information is to be used.
Not insignificantly, the American National Standards Institute (ANSI) approved ISA as an ANSI-accredited standards-writing organization in 1976.
Wireless 802.15.4 enables wireless sensors
The ISA100.11a (IEC 62734) wireless networking technology standard, developed by ISA, focused on “wireless systems for industrial automation: process control and related applications” with a focus on field-level devices. In 2009, the ISA Automation Standards Compliance Institute established the ISA100 Wireless Compliance Institute. The ISA100 Wireless Compliance Institute owns the “ISA100 Compliant” certification scheme, which does independent testing of ISA100-based products to ensure they conform to the standard.
WirelessHART (IEC 62591) is a wireless sensor networking technology based on HART. It is defined for the requirements of process field devices. A goal of WirelessHART is backward compatibility with existing HART-compatible control systems and configuration tools to integrate new wireless networks and their devices.
Machine vision and image recognition
ISA-95 enterprise-control system integration standard B2MML
B2MML is an open source XML implementation of the ISA-95 and IEC 62264 standards. The Manufacturing Enterprise Solutions Association (MESA International) B2MML is used as the de facto standard interface to exchange the contents defined in ISA-95. There is cooperation to bring this into the OPC UA framework, which provides a secure and reliable architecture for manufacturing industries.
Gaming technology
Over the years, the industrial and process automation industry has taken advantage of and leveraged commercial technologies as they became mainstream to create applications that deliver greater value. Augmented reality has seeped into daily life and is being used in everything from mobile games to heavy industry. These innovative technologies can assist with every phase of a project, including design, virtual commissioning, startup, troubleshooting, and quality control. Examples of applications that benefited from these technologies are:
- Machine and process simulation, including virtual commissioning, to identify issues and bottlenecks before installing real equipment, saving time and money
- Smart glasses with immediate access to manuals, instruction videos, and other materials to help on-site personnel troubleshoot problems. Coupled with communications to subject-matter experts at remote sites, this is a tremendous value to improve production uptime.
- Training simulators provide immersion learning to plant personnel before they go on the site. For example, there are many demonstrations of training people in a virtual petrochemical plant environment and giving them challenges, so they learn how to react to dangerous disruptions and operations.
OPC UA
OPC UA can be deployed in any operating system, including Windows, Linux, real-time operating systems, and proprietary systems. Consistent with modern software practice, OPC UA is open source and available on the open source GitHub website.
The basic principles of service-oriented architecture are independent of vendors, products, and technologies for seamless interoperability. OPC UA has become the unifying system architecture to communicate data and information from many industrial automation disciplines efficiently and effectively. Working with various standards groups, the OPC Foundation jointly created standardized information models, defined in Companion Specifications, to achieve interoperability from sensors to enterprise without layers of software for translation and normalization to disparate systems.
Machine learning
The iterative aspect of machine learning is important, because as models are exposed to new data they automatically adapt and learn from previous computations to produce reliable, repeatable decisions and results. Today the ability to automatically apply complex mathematical calculations to big data repetitively with high-performance, low-cost computing is driving applications such as:
- self-driving cars
- Amazon and Netflix online recommendations
- fraud detection.
In the past, applications had to be built from scratch. Now “off-the-shelf” solutions implemented in common open-source frameworks (e.g., TensorFlow, PyTorch, Scikit-learn) make it possible to rapidly create applications.
Predictive maintenance using machine learning is increasing the uptime of manufacturing and process production lines by eliminating breakdowns that by their nature are disruptive unplanned events. By monitoring equipment and benchmarking against models and rules, systems can predict problems and advise maintenance workers to make repairs before problems cascade into larger failures. In addition, embedded processors with sensors are being added to specific pieces of equipment to analyze and alert maintenance about impending problems. Machine learning is also being applied as part of the closed-loop strategy for control and automation to improve machine and process performance.
Industry 4.0 initiatives
A core tenant of Industry 4.0 is that automation systems must adopt open source, multivendor, interoperability software application and communication standards similar to those that exist for computers, the Internet, and cell phones. Industry 4.0 demonstrations acknowledge this by using existing standards, including the ISA-88 batch standards, ISA-95 enterprise-control systems integration standards, OPC UA, IEC 6-1131-3, and PLCopen.
The Industry 4.0 initiative started as one part of a 10-point high-tech German strategic plan created in 2006. On 14 July 2010, the German cabinet decided to continue the strategy by introducing the High-Tech Strategy 2020 initiative focusing the country’s research and innovation policy on selected forward-looking projects related to scientific and technological developments over 10 to 15 years. Industry 4.0 is a vision of integrated industry implemented by leveraging computing, software, and Internet technologies. The 4.0 refers to the idea of a fourth Industrial Revolution:
- First: production mechanization using water and steam power
- Second: mass production (Henry Ford often cited as the innovator)
- Third: digital revolution (e.g., machine tool numerical control, programmable logic controllers, direct digital control, and enterprise resource planning)
- Fourth: Industry 4.0 leveraging cyber-physical systems, embedded computing, Internet of Things technologies
The German strategy emphasizes cooperation between industry and science to promote closer links between knowledge and skills.
The vision of Industry 4.0 is significantly higher productivity, efficiency, and self-managing production processes where people, machines, equipment, logistics systems, and work-in-process components communicate and cooperate with each other directly. A major goal is applying low-cost mass production efficiencies to achieve make-to-order manufacturing of quantity one by using embedded processing and communications. Production and logistics processes are integrated intelligently across company boundaries, creating a real-time lean manufacturing ecosystem that is more efficient and flexible.
The digital twin
The fundamental idea of the digital twin is to have a virtual model of ideal manufacturing operations and processes. This model will benchmark the actual production metrics in real time. The broadest implementation models include all of the factors that affect efficiency and profitability of production, including machines, processes, labor, incoming material quality, order flow, and economic factors. Organizations can use this wealth of information to identify and predict problems before they disrupt efficient production.
The digital twin is a prominent example of practical macro-level, closed-loop control that is feasible with the advanced hardware, software, sensors, and systems technology now available. A critical part of the creation of a digital twin is the need to have a complete information set, including the capture of real-time information with a wide range of sensors based on these requirements. Industry 4.0 is a practical application of the latest technologies, including IoT, to integrate manufacturing and business systems.
Cloud and edge computing
Cloud computing leverages shared resources and economies of scale similar to an electric utility, providing almost limitless computing power and massive storage on demand. Edge computing, a deployment of low-cost and high-performance computing (including communications) is becoming commonplace. It brings computation and data storage closer to the location where it is needed to improve response times, add context to data, and perform functions required locally. In the history of computers and industrial automation, processing has always been pushed as far to the edge of the network as practical with the technology at the time. Today, edge devices can be small blind node computers or SoC embedded in sensors, actuators, and other devices extremely cost effectively. Putting this in context, consider the power and cost of your smartphone today.
These computing devices are platforms for a wide range of software, including IoT, IEC 61131-3 PLC, OPC UA, and MQTT, cloud interfaces, time series databases, HMIs, and analytics. ISA-95 Level 0–2 functions and portions of Level 3 consistent with the new IoT distributed computing models can be accomplished in these devices.
The growing acceptance of industrial sensor networks coupled with edge devices will see more applications deployed on these open system devices rather than PLC and DCS controllers. Edge computing devices deploy both industrial and enterprise networking and communication functions to help seamlessly integrate IT and OT.
Collaborative robots
These robots are particularly attractive investments for small- to medium-sized companies. The programming process of this new class of robots is greatly simplified and does not require programming gurus. The robots can be programmed by example or with software that is similar to gaming. Most tasks can be accomplished with no programming skills simply by moving the robot arms and end effectors, teaching the robot what to do. The robot memorizes the motions and creates the program. This is a physical form of the popular computer concept called “what you see is what you get” (WYSIWYG) programming. It is intuitive for users and has proven to broaden the application of technology. The typical cost is less than $40,000 U.S. Simplified programming means collaborative robots can be deployed without hiring specialized engineers.
The development of this new class of robots is similar to how the application of computers expanded with the development of the PC. In the beginning, computers were expensive, powerful devices locked away in special rooms and programmed by software specialists who wrote cryptic computer code. Because the cost to implement solutions was high, few applications used computers. When PCs were introduced, they did not have the computational power of mainframes and minicomputers nor the large amount of memory. But with their lower cost and flexibility, people were empowered to apply computers to a wider range of applications. This factor, coupled with simplified programming, led to a revolution in the application of computers for industrial automation.
These new collaborative robots cannot pick up an engine block, but they can perform a great variety of tasks with smaller payloads, typically 10–30 kilograms. Collaborative robots can flawlessly perform repetitive, mundane, and dangerous tasks that were previously performed by an operator. Operators no longer are forced to stand at a machine for hours doing mindless work or working in a hazardous environment. This improves productivity and quality while freeing up workers for tasks that require human skills.
Cobots are now one of the fastest-growing industrial automation segments; it is expected to jump tenfold to 34 percent of all industrial robot sales by 2025, according to the Robotic Industries Association (RIA) (www.robotics.org/blog-article.cfm/Collaborative-Robots-Market-Update-2018/84). An exciting development is the coupling of collaborative robots with vision systems, image recognition, and artificial intelligence that replicate human manufacturing procedures.
Collaborative robots have lowered the barriers to automation. A broad range of users, particularly small and medium enterprises, can implement them without sophisticated automation personnel. The flexibility of collaborative robots enables the automation of functions that were not practical in the past. Collaborative robots are also suitable for production with make-to-order requirements, since they are easily programmed to do multiple tasks.
Titans of Automation
Walter Brattain and William Shockley, transistor inventors
Federico Faggin, microprocessor innovator
Richard Rimbach, ISA founder and first secretary
Albert F. Sperry, ISA founder and first president
Glenn F. Harvey
A. T. James and A. J. P. Martin, gas-liquid chromatograph
Dick (Richard) Morley, father of the PLC
Morley and his team of engineers developed a solid-state, sequential logic solver designed for factory automation and continuous processing applications: the first practical programmable logic controller called the Modicon 084. The company demonstrated the Modicon 084 to General Motor’s Hydramatic Division in 1969 and delivered the first commercial unit to GM in 1970 to control metal cutting, hole drilling, material handling, assembly, and testing for the Hydramatic Model 400 automatic transmission. The new system replaced the large electromagnetic relay panels that GM previously used to identify where problems had occurred.
The PLC allowed those in the control industry to program the system, which was not possible with electromagnetic relay panels.
Karl Åström, father of adaptive control
Bill Gates and Paul Allen, Microsoft founders
Larry Evans, pioneer in process modeling
When the project was completed in 1981, Evans, along with seven key members of the project staff, founded Aspen Technology, Inc. (AspenTech) to license the technology from MIT and to further develop, support, and commercialize it. As CEO at AspenTech, Evans greatly expanded the breadth and depth of the technology over the ensuing years and brought on board a wide range of complementary products. The company grew from a 10-person startup to a public company.
Dennis Morin, founder of Wonderware
In one of the great rags-to-riches entrepreneurial stories of the 1980s, Morin was 40 years old when he was terminated by Triconex and started Wonderware. He drove a taxi in Boston before coming to California in the 1970s. He told his idea to a young technology wizard, Phil Huber, who joined him in forming Wonderware.
Patrick Kennedy, father of plant historians
Kennedy earned a BS and a PhD in chemical engineering from the University of Kansas. A registered professional engineer in control systems engineering, he holds a patent on a catalytic reformer control system.
Tom Fisher, champion of ISA-88
Lynn Craig, champion of ISA-88
Dennis Brandl, champion of ISA-95
Ed Hurd, helped birth commercial DCS
Ed Hurd was a major driver of the Honeywell 2000, which was introduced in 1975 and marked the beginning of commercial DCSs. At the 1976 ISA show in Houston’s Astrodome, Honeywell formally unveiled the TDC-2000, the first system to use microprocessors to perform direct digital control of processes as an integrated part of the system. This distributed architecture was revolutionary with digital communication between distributed controllers, workstations, and other computing elements. Hurd served as president of Industrial Control from 1993 to 1995 and, before that, was vice president and general manager of Honeywell’s Industrial Automation and Control Group. He won a Sweat Award in 1967 for circuitry design and was the design architect for an assignment called Project 72. After about two years, the group synthesized a next-generation control system. The project led to the TDC 2000, a DCS that took the industrial automation and control group from $5 million to $500 million in five years.
Bill Lowe, lab director for the IBM PC
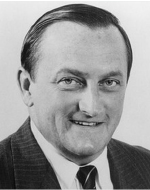
John Berra, communication protocol impresario
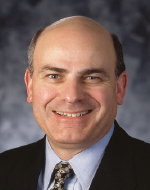
Charlie Cutler, redefined APC
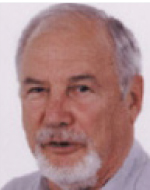
Odo Struger, named the PLC
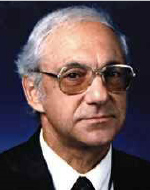
Mike Marlowe, U.S. federal government liaison for ISA

Peter G. Martin, automation renaissance man
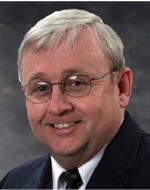
Vint Cerf, father of the Internet
Reader Feedback
We want to hear from you! Please send us your comments and questions about this topic to InTechmagazine@isa.org.